在波音公司宣布将600多件3D打印部件用于波音的Starliner太空出租车之时,我们不由得感叹于塑料代替轻质金属合金将成为交通工具领域的一大趋势。而最近在国内,南京航空航天大学在连续纤维增强热塑性树脂打印技术取得了创新突破。
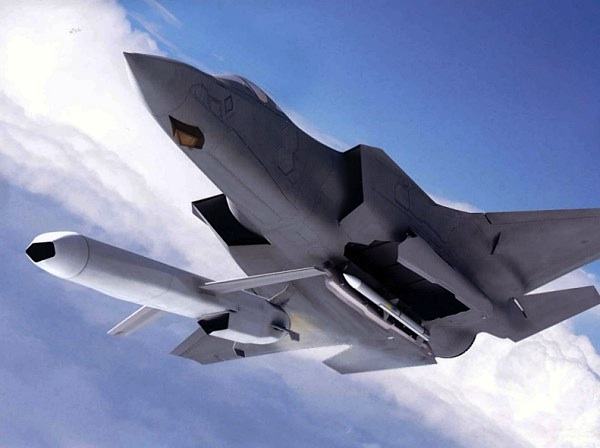
熔融沉积成型(FDM)技术凭借其较低的成本和较优异的可实现性,近年来取得了很大的市场占有率。但该工艺使用可加热融化的热塑性树脂耗材为成型材料,材料本身不具有连续性,层内分子团间距较大,且逐层铺叠的工艺特点也造成了较差的层间结合力,这些特点都导致零件脆性大,冲击强度低,易变形,承载性能差。
国际和国内通常在零件的设计过程中采用结构拓扑优化的方式来优化力学性能,亦或是在热塑性基材中加入颗粒,短切纤维等增强体,终究不能根本上提高熔融沉积工艺所成型构件的力学性能。特别是针对航空航天领域内的复杂构件,轻量化和高强度的要求日益严苛,虽然熔融沉积等增材制造工艺可以大幅度的节省原材料,降低零件制造的难度,但其制品力学性能较差也是限制其在行业内发展的主要原因。
市场上的连续纤维增强树脂基复合材料的3D打印方法存在以下主要问题:
各类纤维在出厂时,其表面活性基团均只适应于与热固性树脂的浸润过程。在使用简单的措施将未处理的纤维与熔融热塑性树脂共混时,难以使纤维与树脂充分浸润,这导致构件的纤维-树脂界面较差。
大丝束纤维呈展平带状,现有3D打印方法难以使用大丝束纤维,且小丝束纤维在成型过程中成型速度慢,成型后的表面质量、纤维树脂体积分数、纤维树脂分布情况、层间结合力等性能指标难以控制。
现有的方法在打印过程中,由于纤维的局部分叉、断裂,容易造成纤维在腔体中堆积、堵塞,对成型过程造成影响,同时,成型轨迹中纤维呈松散、无规律的分布状态,使得构件的承载性能受到影响。
南京航空航天大学发明了连续纤维增强热塑性树脂基复合材料的3D打印方法。适用于尺寸较大的纤维丝束,该打印技术成型速度快,表面质量提高,同时纤维与热塑性基体间的界面结合性能好,构件纤维含量高,纤维密实度高,并且提高了打印构件的力学。还研发出连续纤维增强热塑性树脂基复合材料旋转共混3D打印头,其特征在于:挤出头连接于熔融腔也可绕中轴旋转,且旋转方向与熔融腔相反;熔融腔与挤出头内侧均有搅拌齿环,纤维束和熔融热塑性树脂受到两级反向旋转的螺旋齿环搅拌作用下均匀共混,且共混体以螺旋状密实缠紧成圆柱丝束,树脂沿纤维取向均匀分布;挤出头挤出材料至成型区域并固化成纤维增强树脂基复合材料。
采用两级旋转腔体对纤维和树脂的共混体进行搅拌和缠绕,适用于较大尺寸的纤维丝束,优化了打印头对纤维原有状态的适应性,在相同的打印速度下,提高了打印效率,改善了构件的表面质量;搅拌共混的作用下,纤维与树脂间的浸润充分,共混体中的纤维呈紧密螺旋缠绕状,提高了增强体的承载能力,树脂在纤维中各处分布均匀,改善了构件的层间和界面结合性能,提高了打印构件的力学性能;挤出头的旋转作用可使共混体在挤出后,纤维与树脂的分布均匀,纤维体积含量高。
实现了较高力学性能连续纤维增强热塑性基体复合材料构件的3D打印,且成型效率高,表面质量好,可适用于对性能要求较高的航空航天复杂构件的成型过程。
|